BREITNER –
Packaging machines Glossary
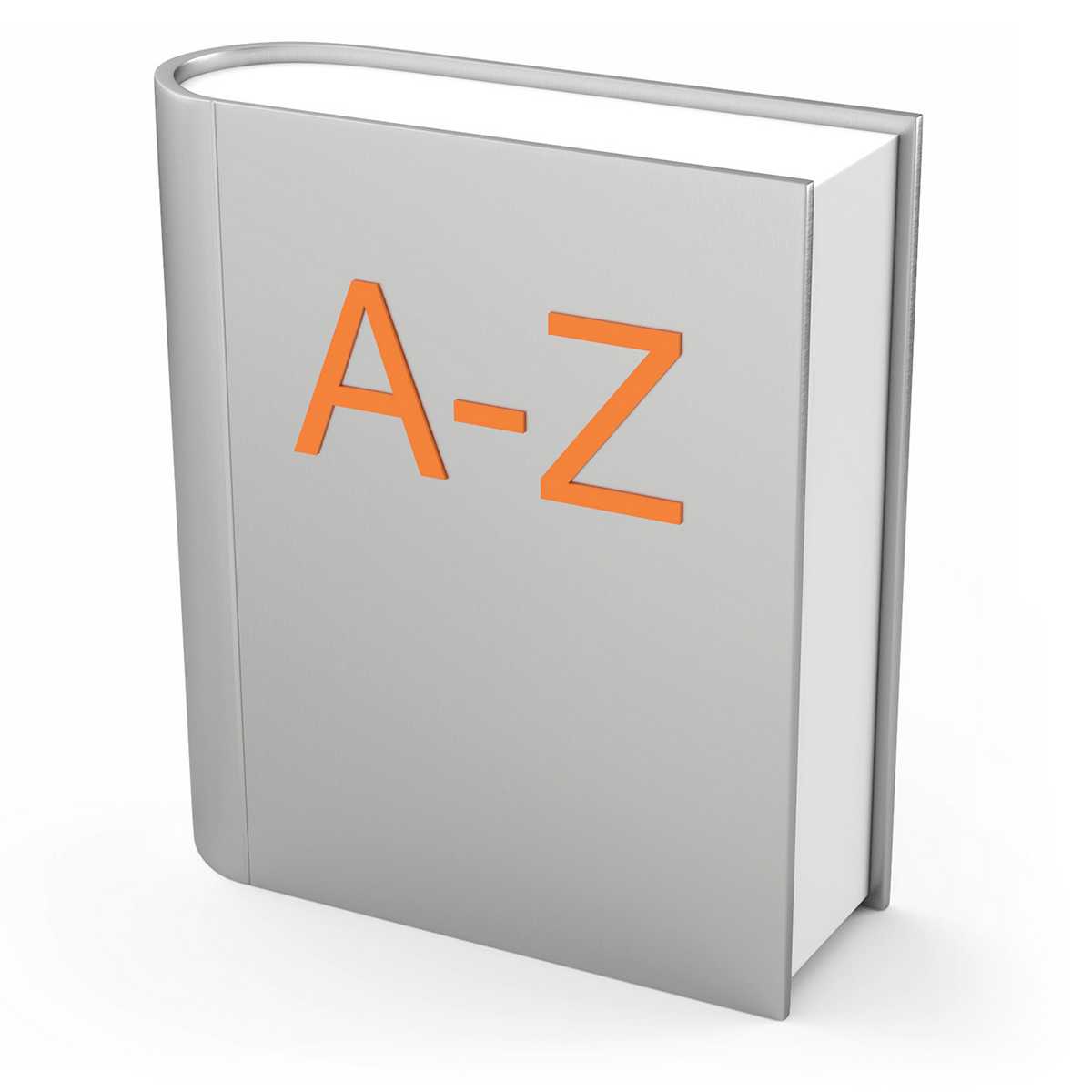
This packaging machine glossary is not a universal lexicon, but explains technical terms in the context of the BREITNER products and with a view to the experience, focus and engineering in our company. Therefore, the glossary also contains references to process-related advantages or special features of our products and services.
Terms with a -> right arrow are explained at the corresponding alphabetical position. We have – admittedly – refrained from using machine links for reasons of effort.
A note: Your browser supports you in the search (Ctrl + F).
Above level filling
During the filling process, the liquid level rises continuously. In the case of above level filling, the -> machine control ensures that the mouth of the filling nozzle is always at the same distance above the -> liquid level. This is also the case with waisted bottles (-> moulded bottle), where the rise in the liquid level fluctuates in the course of the filling process. In particular, the output rate is optimised because the product flow into the container is stabilised.
Agitator
An agitator in the -> product vessel keeps the product homogeneous in terms of consistency or temperature. In practice, products that require an agitator often have the following characteristics:
- they are lumpy, such as fondue sauces
- they have to be filled hot, e.g. jam
- they sediment easily.
Bayonet closure
-> closure
Below level filling
Here, the same applies as for -> above level filling, whereby the filling nozzle is always located just below the liquid level. In this way, foaming products are prevented from foaming.
Blow-out station
The blow-out station is one of the work stations inside the -> bottle unscrambler. Here, the bottles are blown out upside down from below with compressed air and thus cleaned of particles, such as residues from production or dust.
Bottle unscrambler
The bottle unscrambler transports the unsorted bottles from the storage bunker and places them in the correct position and, in the case of asymmetrical bottles, “nose first” on the conveyor belt.
Special shapes or options offer additional functions, e.g. cleaning of the bottle (-> blow-out station) or insertion into a -> transport form.
Cleaning cup
Cleaning cups are pushed over the filling nozzles from below during cleaning of the machine (->CIP, -> SIP). They get their name from the goblet-shaped design with which they neatly seal off the filling nozzle from the surroundings. This seals the circuit of the cleaning or rinsing medium or the hot steam at the filling position.
CIP (Cleaning in Place)
Cleaning in Place (CIP) is implemented throughout the design of the BREITNER -> filling machines. The machine does not have to be dismantled for cleaning; instead, the cleaning and rinsing medium is fed through the machine via supply and drain lines. It reaches all points within the product guide of the machine where cleaning is required. Special design measures are required at some points, e.g. in the area of the drive for the dosing piston (piston backflushing).
Closing machine
The closing machine is used to close the filled and still open containers. BREITNER supplies
- -> Linear closing machines
- > Rotary closing machines.
Closure
The -> closing machines from BREITNER process a wide range of closure designs: Push-on closures, screw closures, insertable stoppers and droppers, flat lids, bayonet closures. A particular advantage is the processing of different shapes of closures with -> dip tubes. Combinations of up to three closures in succession (e.g. dropper, screw closure and dust cap) can also be processed.
Container
Container is a collective term that covers all containers from the small 20 ml bottle to the 40 l canister. Due to the great flexibility of BREITNER machines – there are no pure bottle or canister machines – this collective term has proven itself.
Note: When BREITNER refers to the -> vessel, it means the -> product storage vessel.
Dip tube
Closures with dip tubes are found on bottles for cleaning agents (spray pumps) or soap dispensers. When closing the container, the dip tube must be threaded into the often narrow bottle neck – a technical challenge at a high output rate. This is where BREITNER technology shows its particular advantages.
Dosing principles
BREITNER machine control systems use three different dosing principles to determine the filled quantity (volume or mass of the filled -> product):
- -> Inductive flow measurement (volume measurement)
- -> Mass flow measurement (Coriolis force measurement) (measurement of mass)
- -> Piston dosing (volume measurement).
In special cases, peristaltic pumps (volume measurement) are used.
Dosing range
The dosing range indicates the range between the smallest and largest quantity that can be filled at a -> filling station. A typical value is 50 ml to 1000 ml, which means a range of 1 to 20. The larger this range, the more flexible the machine can be used. The dosing range is determined by the -> dosing principles and the associated measuring device and the mechanics of the machine. A margin of 1 to 40 is quite feasible under certain circumstances.
Empty container monitoring
Empty container monitoring is a sensor-supported test function of the machine control directly at the filling position. This ensures that there is actually a completely empty container under a filling position. This check is important after a machine stop to ensure a clean filling operation even when the machine is restarted.
Explosion (Ex)-protection
Explosion-protected machines are designed in accordance with EC Directive 2014/34/EU (ATEX). They are used for filling and closing highly flammable liquids such as disinfectants, petroleum ether, alcohol or other products containing solvents.
Explosion protection requires a whole range of technical measures. These range from specially approved components to -> source extraction and connection to the on-site -> extraction system. With a view to the subsequent acceptance of the machine, elaborations for -> zone classification as well as documentation tasks are required in the planning phase.
Extraction system
In systems that fill under -> explosion-proof conditions, the gases that are released during the filling process are discharged from the point of emission – at the opening of the filling nozzle – to the suction system provided on site.
Filling machine
The filling machine is used to fill the liquid -> product into -> containers. Depending on the product, there are various principles for -> dosing to choose from. BREITNER supplies machines with -> flow measurement as well as -> piston filling machines. In addition, we also offer special machines that allow other forms of dosing, e.g. via peristaltic pumps.
Filling nozzle
The filling nozzle dips into the bottle neck and guides the -> product to the liquid level. At the end of the filling process, the filling nozzle can be closed at the front end – this completes the filling process precisely and cleanly.
Filling position / filling station
Each filling position in a filling machine fills a single -> container during a work cycle. The number of filling positions thus determines the -> output rate. Each filling position has its own flow meter or dosing piston, so that precise dosing is ensured at each individual filling position.
Flow measurement
Two methods are used for flow measurement
- -> Inductive flow measurement
- -> Mass flow rate measurement.
Inductive flow measurement
The measuring method of inductive flow measurement is based on the principle of electromagnetic induction. The (conductive) liquid flowing through the measuring tube is brought into a magnetic field. This magnetic field generates a voltage in the liquid transverse to the direction of flow, which is proportional to the flow velocity and can be measured at electrodes embedded in the measuring tube.
Insertion station
The insertion station is a work station within the -> closing machine. Here, stoppers or droppers are pressed into the container opening from above.
Lid inspection
The lid inspection after the closing station within the -> closing machine checks whether the container is actually properly screwed down. Such checks can be carried out by various technical measures such as light sensors or monitoring of the -> servo drive at the -> screw closing station.
Line output
The line output is the -> output rate of the entire packaging line, consisting of bottle unscrambler, filling and closing machine.
Linear closing machine
A linear closing machine has a linear structure (in contrast to the -> rotary closing machine). The containers run into the machine linearly on a conveyor belt, are stopped under the closing spindle and closed individually. Alternatively, the containers are transferred to a transport starwheel, which fixes them precisely at the workstation(s). After closing, they leave the machine on the conveyor belt.
Note: With the closing machine type VSL, the (usually) canisters run through the machine without stopping and are closed by a closing spindle that runs with the canister.
Linear filling machine
A linear filling machine is characterised by a linear design (in contrast to the -> rotary filling machine). The containers run into the machine linearly on a conveyor belt, are stopped under the filling nozzles, filled and transported onwards at the end of the filling process.
Liquid level
During the dosing process, the liquid level in the container rises. In order to carry out the filling process as quickly and cleanly as possible, the -> filling nozzle moves upwards as the liquid level in the bottle rises. The -> machine control ensures that the distance between the opening of the filling nozzle and the liquid level remains constant in order to optimise the filling process. If the opening of the filling nozzle is just above the liquid level, this is called -> above-level filling; if it is just below, it is called -> below-level filling.
Machine control
The machine control system of the BREITNER machines contains the control of the machine functions themselves as well as the control of the user interface with the operating functions.
A particular advantage of the control system is the large number of intelligent functions that support and monitor the filling and closing process. The associated control algorithms – especially for filling – are based on the company’s decades of experience and shape the functional advantages of the machines.
Mass flow measurement (Coriolis force measurement)
The mass flow measurement method uses the physical principle of Coriolis force. The – moving – mass flow in the curved measuring tube is caused to oscillate from the outside at right angles to the direction of flow. These two mutually perpendicular movements generate a phase shift via the Coriolis force, which can be detected by sensitive sensors and which is proportional to the flow velocity of the moving mass.
Mould inserter
The mould inserter in the -> bottle unscrambler inserts a bottle into a -> transport mould (puck). The bottle and the mould are then placed on the conveyor belt. This is necessary for bottles that are not sufficiently stable on the conveyor belt or to save -> size parts.
Output rate
The output rate, measured in containers per minute, indicates the throughput of the individual machines. The data on the website represent typical upper limits that are set by the machine technology itself. Depending on the -> product or also on the size or geometry of the -> container or -> closure, this value decreases.
Piston dosing
A -> piston filling machine is characterised by the fact that the filling product is dosed by the stroke of the piston in a cylinder. The dosed product volume is thus proportional to the stroke height of the piston. If the dosing volume is smaller than half the piston content, several containers can be filled with one filling of the piston (improvement of the -> output rate). If the dosing volume is larger than the piston, the container is filled with several strokes (but at the expense of the output rate). This means that a comparatively large -> dosing range can also be achieved with a piston filling machine.
Piston filling machine
A piston filling machine works with -> piston dosing as dosing principle.
Press-on cap
-> closure
Press-on station
The press-on station is located inside the -> closing machine as a work station; here, press-on closures are pressed onto the container opening from above.
Pressure vessel
-> product vessel
Product
“Product” is the collective term for all liquids, creams, pastes, honey, etc. that are filled and packaged on BREITNER machines. The spectrum of products that can be processed with BREITNER machines with their specific properties is wide: viscosity, homogeneity, possible foaming, special requirements for the temperature during filling are just a few product parameters that must be considered when designing filling systems. In this way, an optimum result can be achieved in terms of cleanliness and output rate.
Product (storage) vessel
The product vessel serves as a buffer vessel on the filling machine. It is used unpressurised (-> piston filling machines) or pressurised (-> flow measurement). Depending on the product, the container can be equipped with different options, such as heating, agitator or special provisions for cleaning.
Rotary closing machine
A rotary closing machine is a closing machine with a circular design (in contrast to the -> linear closing machine). The containers run through the machine without stopping and are simultaneously screwed by up to 12 capping spindles. The high -> output rate resulting from this is particularly advantageous for large batch sizes (e.g. cleaning agents).
Note: The closing machine type SRT also allows closing at a high output rate for closures with dip tubes.
Rotary filling machine
A rotary filling machine is a filling machine with a circular design (in contrast to the -> linear filling machine). The containers run through the machine without stopping and are filled simultaneously from up to 30 filling positions. The high -> output rate resulting from this is particularly advantageous for large batch sizes (e.g. cleaning agents).
Screw closing (capping) station
The screw closing station is a work station in a -> closing machine where a screw closure is applied. This can be a simple screw closure or a closure where the angle of rotation must be considered when screwing (-> servo drive).
Note: A particular advantage of BREITNER machines is the screwing of spray pistols with -> dip tubes.
Screw closure
-> closure
Servo drive (screw spindle)
A servo drive, in contrast to a drive with an asynchronous motor, offers a number of advantages in the screwing process:
- It allows precise angular movement (bayonet lock).
- The control of speed and torque support the monitoring of screwing in the process.
- Changeover to other container and closure shapes is easy, just by changing the control parameters of the servo drive.
Shaped bottle
Shaped bottles are containers that have a distinctive bottle shape in order to fulfil a certain function (example: handle of an all-purpose cleaner bottle) or in order to make the brand reference haptically clear; they are often asymmetrical. When transporting shaped bottles through the plant, their shape must be considered. Examples:
- Is it sufficiently stable and can it be stowed or does it need a transport shape?
- Does the bottle unscrambler have to align an asymmetrical bottle so that it runs through the machine “nose first”?
- Does a special filling profile have to be specified during the filling process to ensure clean under- or over-level filling?
Single container detection
With single container detection, sensors ensure that a container is correctly positioned under each -> filling nozzle at the start of the dosing process. This improves reliability for smooth filling processes.
SIP (Sterilisation in Place)
Sterilisation in Place (SIP) allows – in addition to cleaning ( -> CIP, Cleaning in Place) – sterilisation of the machine. In this process, -> superheated steam is passed through the product guide, which kills the germs at the appropriate temperature and for the appropriate time. The filter device of the compressed air supply, which is required for operation, can also be sterilised
Size part
Size parts are accessories for the machine that also have to be replaced when changes are made in the filling or capping process, e.g. when the container is changed. These include, for example, the filling nozzle (larger diameter when filling into canisters) or the transport starwheel (precise fixing of the bottle during closing).
Linear filling and closing machines generally require fewer size parts than rotary filling and closing machines. The latter, however, deliver a higher -> output rate.
Source extraction
With source extraction, product vapours are extracted that escape at the container opening during filling. Particularly when filling under explosion protection conditions, it is important that these vapours are passed on as directly as possible to the production hall’s on-site extraction system.
Stopping slide
The stopping slide stops containers on the conveyor belt for filling or closing. Special stopping slides are available for particularly heavy (canisters) or soft containers.
Superheated steam
Superheated steam is used in -> sterilisation (SIP) of a filling machine to kill off any germs present as completely as possible. The temperature is over 120°C.
Thread cutter
The thread cutter cuts the remaining “product thread” of a highly viscous -> product shortly after the end of dosing. This increases the -> output rate because the following filling process can start more quickly.
Throughput
-> Output rate
Transport form / transport mould (puck)
A transport form carries bottles that have insufficient stability of their own on the conveyor belt or cannot be accumulated for reasons of their geometry (“wide shoulder”). Another advantage: transport forms having always the same outer dimensions help to reduce size parts or simplify changeovers even with different bottle shapes.
Note: The BREITNER bottle unscrambler type BFP supports insertion into transport forms.
Transport starwheel
In the intermittently operating closing machines, a transport starwheel fixes the container in such a way that the container neck is precisely positioned under the -> screw closing station when screwing. This is particularly important for closing machines that apply several closures in succession (stopper/dropper, screw closure, dust cap/measuring cup).
Turning station
The turning station of the ->bottle unscrambler turns asymmetrical containers by 180°; they then run through the machine “nose first”.
Twin screw
A twin screw consists of two counter-rotating screws that can reliably and precisely pick up and transport even a soft and less dimensionally stable -> container.
User administration
The machine control system contains a user administration. In this way, the access of the different users – from the machine operator to the setter – to the different operating levels is defined within the software of the -> machine control.
Validation/Qualification
In pharmaceutical applications, proof – together with documentation – is required that the material in the product guide (steel, tubing material, seals, …) meets the requirements resulting from the product (e.g. FDA conformity of plastics). Functional tests (e.g. detection of an incorrect screwing due to a defect on the closure, ejection on ID tape) also play a role here.
Vessel
-> Product vessel
Vessel pressure
The vessel pressure inside the -> product vessel must be about 0.5 to 2 bar above the atmospheric pressure when dosing via flow measurement. This pressure difference causes the product to flow from the vessel to the filling nozzle and into the container. This pressure must be kept as constant as possible in order to achieve uniform dosing and thus high accuracy.
Viscosity
“Viscosity” refers to the viscosity of liquids: Honey has a higher viscosity than tap water.
High-viscosity ->products are preferably filled with a -> piston filling machine; for products with lower viscosity, filling machines with -> flow measurement offer advantages for -> dosing.
Zoning
For systems with explosion protection, Directive 1999/92/EC provides for zone classification according to zones 0 to 2; it is the operator’s responsibility to determine these zones. The required technical measures on the machines and the infrastructure in the production hall are based on this.
Are you interested in our filling systems or our packaging machine service?
Then contact us …
Our qualified team will be happy to answer your questions or concerns.